Από τον
Θάνο Αμβρ. Φελούκα
19/1/2019
Η τεχνολογία του 3D Printing μπορεί να φέρει εντυπωσιακές αλλαγές και νέες δυνατότητες στην κατασκευή μοτοσυκλετών, όπως έκανε πριν μία δεκαετία η τεχνολογία της κατασκευής εξαρτημάτων από carbon fiber. Το Honda Monkey της γαλλικής VIBA Motor που είδαμε στην φωτεινή έκθεση Bike Expo μπορεί να μην σκίζει από ομορφιά, όμως η Lazer 3D Printing τεχνολογία που χρησιμοποιήθηκε για να κατασκευαστεί το ρεζερβουάρ και η εμπρός μάσκα, πραγματικά αξίζει την προσοχή μας. Για να αντιληφθούμε τις νέες δυνατότητες που έχουν οι σχεδιαστές με αυτή την τεχνολογία, θα πρέπει πρώτα να καταλάβουμε πως φτιάχνεται ένα εξάρτημα με Lazer 3D Printer. Όλα φυσικά ξεκινούν με την σχεδίαση του εξαρτήματος σε ένα τριδιάστατο σχεδιαστικό πρόγραμμα. Μετά χρειάζεσαι σε μορφή σκόνης το μέταλλο που θέλεις να χρησιμοποιήσεις.
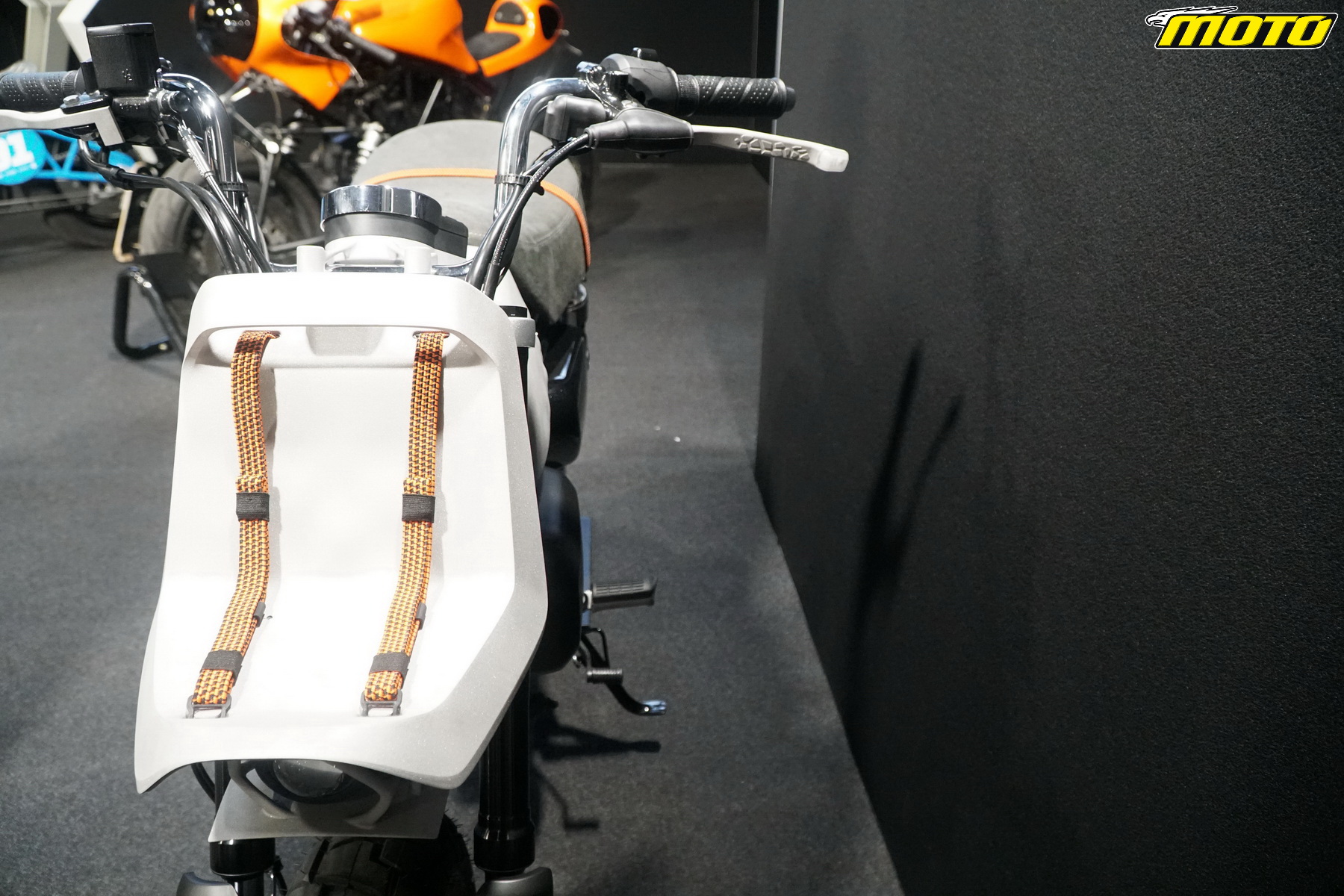
Στην συγκεκριμένη περίπτωση του Monkey χρησιμοποιήθηκε ένα κράμα αλουμινίου που χρησιμοποιούν στην αεροναυπηγική. Τοποθετείς τη σκόνη μετάλλου σε ένα δοχείο σε σχήμα κύβου και μια ακτίνα Lazer αρχίζει να το λιώνει στο σημείο που θέλεις και στην κατάλληλη θερμοκρασία. Έτσι σιγά-σιγά αρχίζει να σχηματίζεται το αντικείμενο που έχεις σχεδιάσει. Όταν η διαδικασία τελειώσει, βγάζεις το εξάρτημα μέσα από τον κύβο και το φυσάς για να το καθαρίσεις από την υπόλοιπη σκόνη μετάλλου που δεν έλιωσε το Lazer. Αυτό το τελευταίο στάδιο μοιάζει πολύ σαν την χύτευση σε καλούπια άμμου, μόνο που εδώ δεν χρειάστηκαν καλούπια και κυρίως δεν χρειάστηκε να σχεδιαστούν δίοδοι για να περάσει το λειωμένο μέταλλο. Το πλεονέκτημα από την απουσία χρήσης καλουπιών είναι κυρίως η ασφάλεια που δίνει αυτή η μέθοδος στον κατασκευαστή πως δεν θα εγκλωβιστεί πουθενά αέρας, οπότε η αντοχή του εξαρτήματος θα είναι ακριβώς αυτή που είχε υπολογίσει όταν το σχεδίαζε. Αυτό με την σειρά του βοηθάει στη μείωση του βάρους, καθώς χρησιμοποιείς μόνο όσο υλικό χρειάζεσαι και δεν βάζεις παραπάνω για να έχεις το κεφάλι σου ήσυχο.
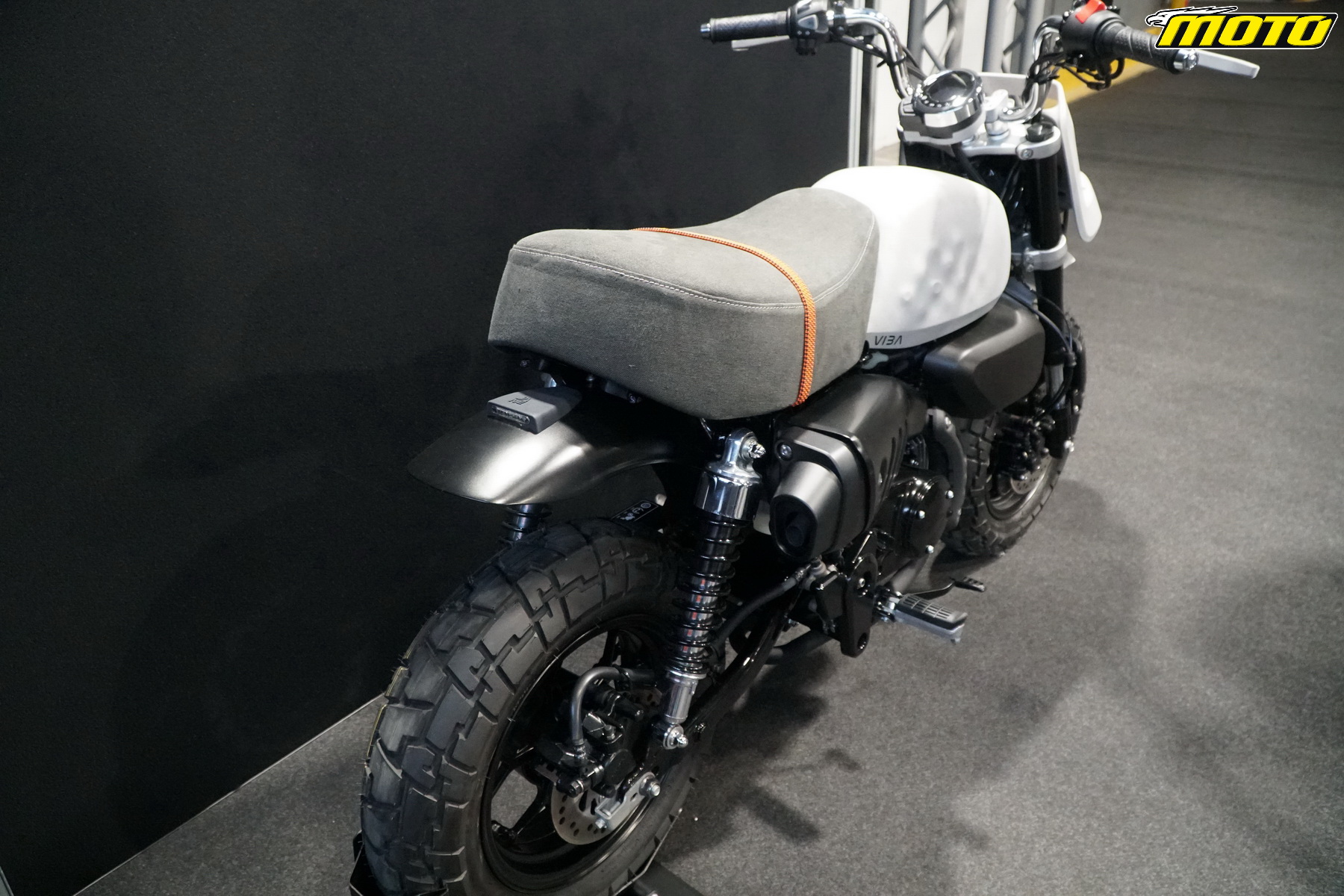
Πράγματι, το 3D Printed αλουμινένιο ρεζερβουάρ του Monkey είναι 10% ελαφρύτερο από ένα συμβατικό αλουμινένιο ρεζερβουάρ, παρά το γεγονός πως στο εσωτερικό του έχει μεταλλική κυψέλη για να περιορίζει την μετατόπιση της βενζίνης!
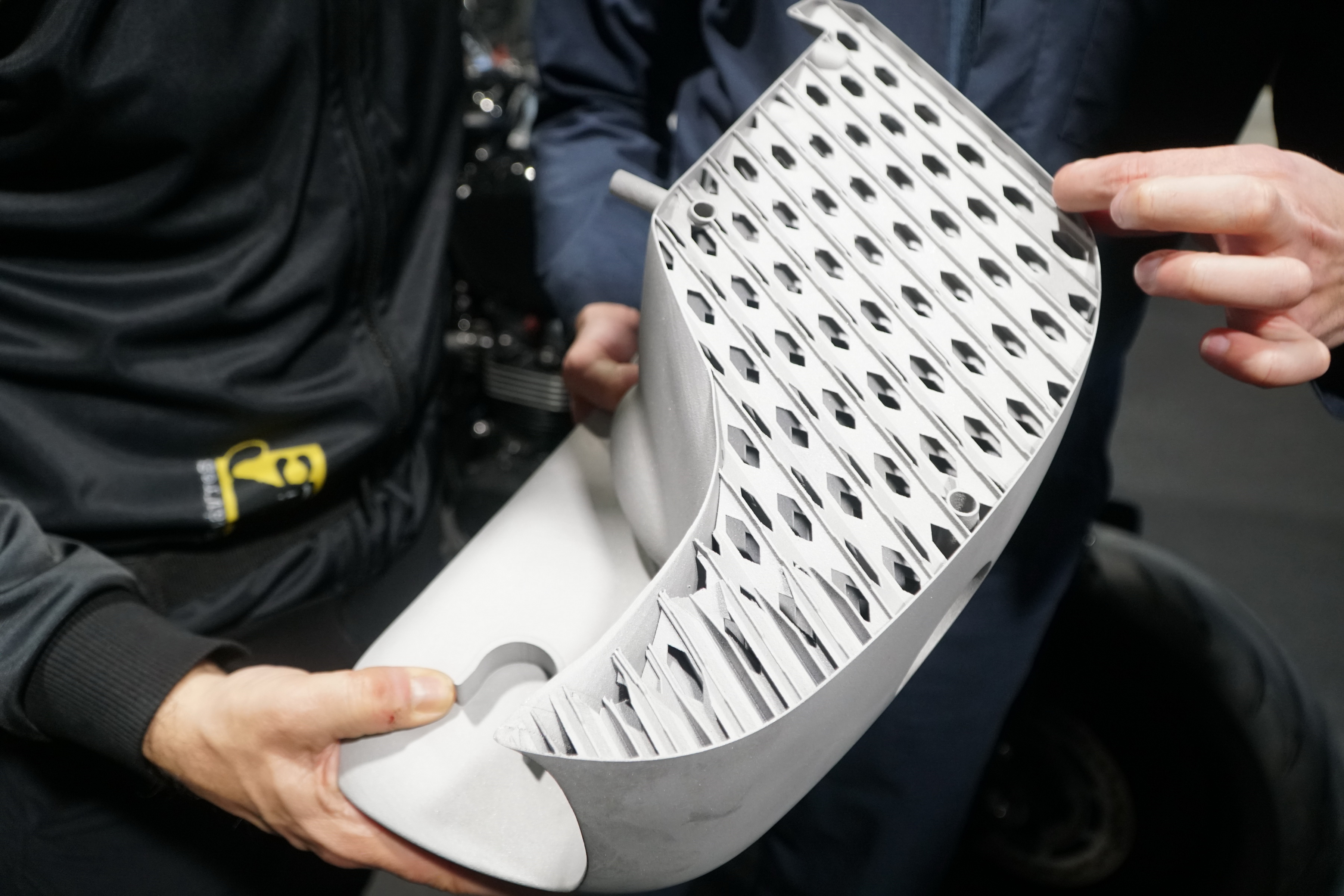
Εδώ είναι το δεύτερο και πιθανότατα σημαντικότερο όλων, πλεονέκτημα αυτής της νέας τεχνολογίας. Η δυνατότητα δηλαδή να φτιάχνεις μονοκόμματα μεταλλικά αντικείμενα σε οποιοδήποτε σχήμα θέλεις χωρίς να χρειάζονται κολλήσεις. Αυτό πράγματι αλλάζει τα δεδομένα κατά τον σχεδιασμό των μοτοσυκλετών, αφού πλέον μπορείς να φτιάξεις περίπλοκα σε σχήμα εξαρτήματα χωρίς περιορισμούς. Για παράδειγμα το αλουμινένιο τιμόνι είναι κούφιο και όλα τα καλώδια και οι ντίζες περνάνε εσωτερικά.
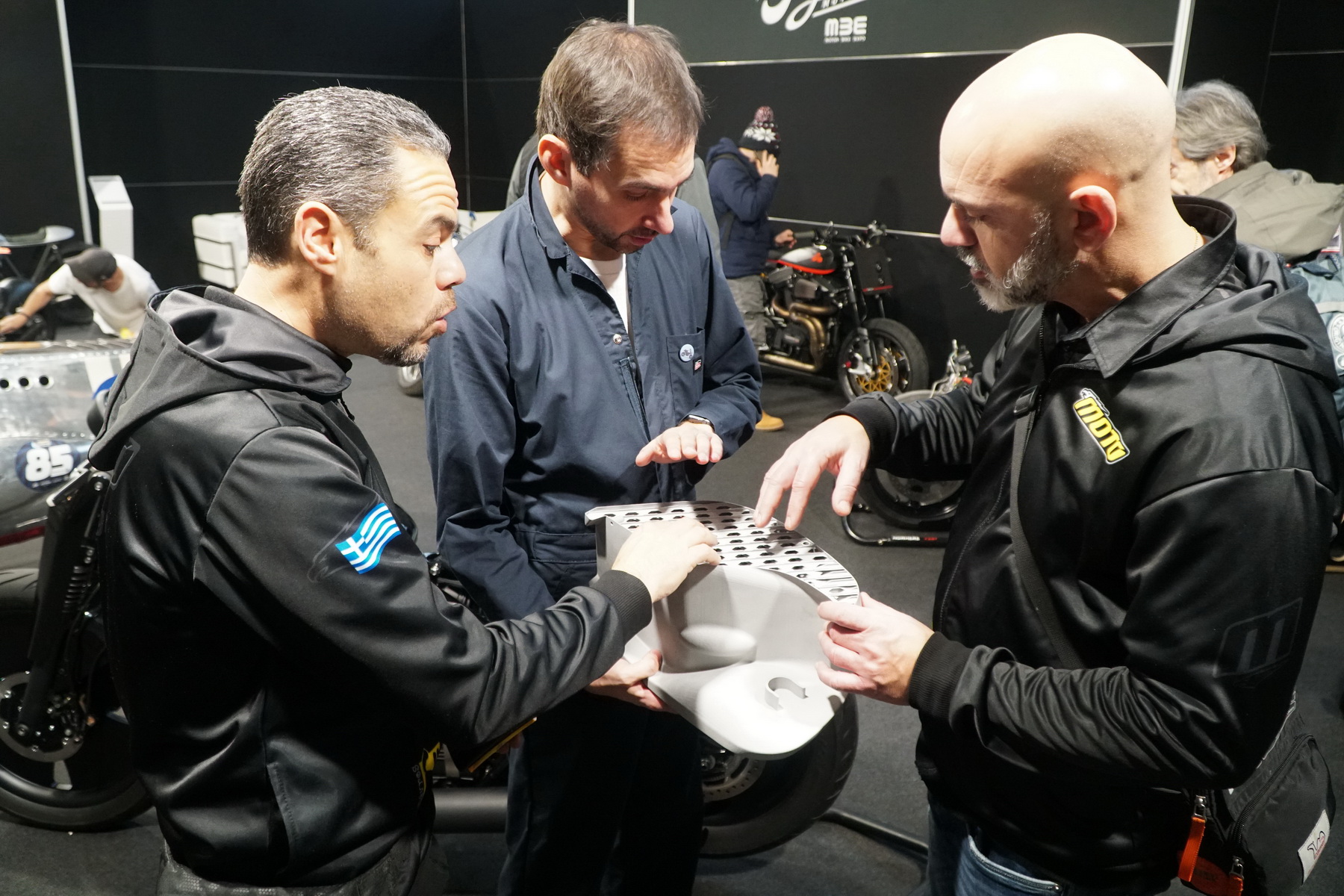
Υπάρχουν φυσικά και μειονεκτήματα, τα οποία όμως είναι βέβαιο πως θα λυθούν στο μέλλον, όπως έγινε και με την τεχνολογία των carbon fiber κατασκευών. Μιλάμε κυρίως για την ταχύτητα της διαδικασίας παραγωγής που προς το παρόν δεν μπορεί να συναγωνιστεί τις παραδοσιακές μεθόδους της χύτευσης των μετάλλων. Αυτό με την σειρά του επηρεάζει το τελικό κόστος, που στην περίπτωση του Monkey είναι 3.000 ευρώ για το ρεζερβουάρ μόνο! Προς το παρόν, 3D Lazer Printed εξαρτήματα σε όχημα ευρείας παραγωγής χρησιμοποιεί η BMW για τον μηχανισμό της ανοιγόμενης οροφής του i8 Roadster. Μάλιστα ακριβώς στον ίδιο Lazer 3D Printer στην Γαλλία φτιάχτηκαν και τα εξαρτήματα του συγκεκριμένου Monkey, από μια εταιρεία που έχει αναπτύξει αυτή την τεχνολογία πολλά χρόνια πριν, καθώς είναι προμηθευτής των μαχητικών αεροσκαφών Mirage.
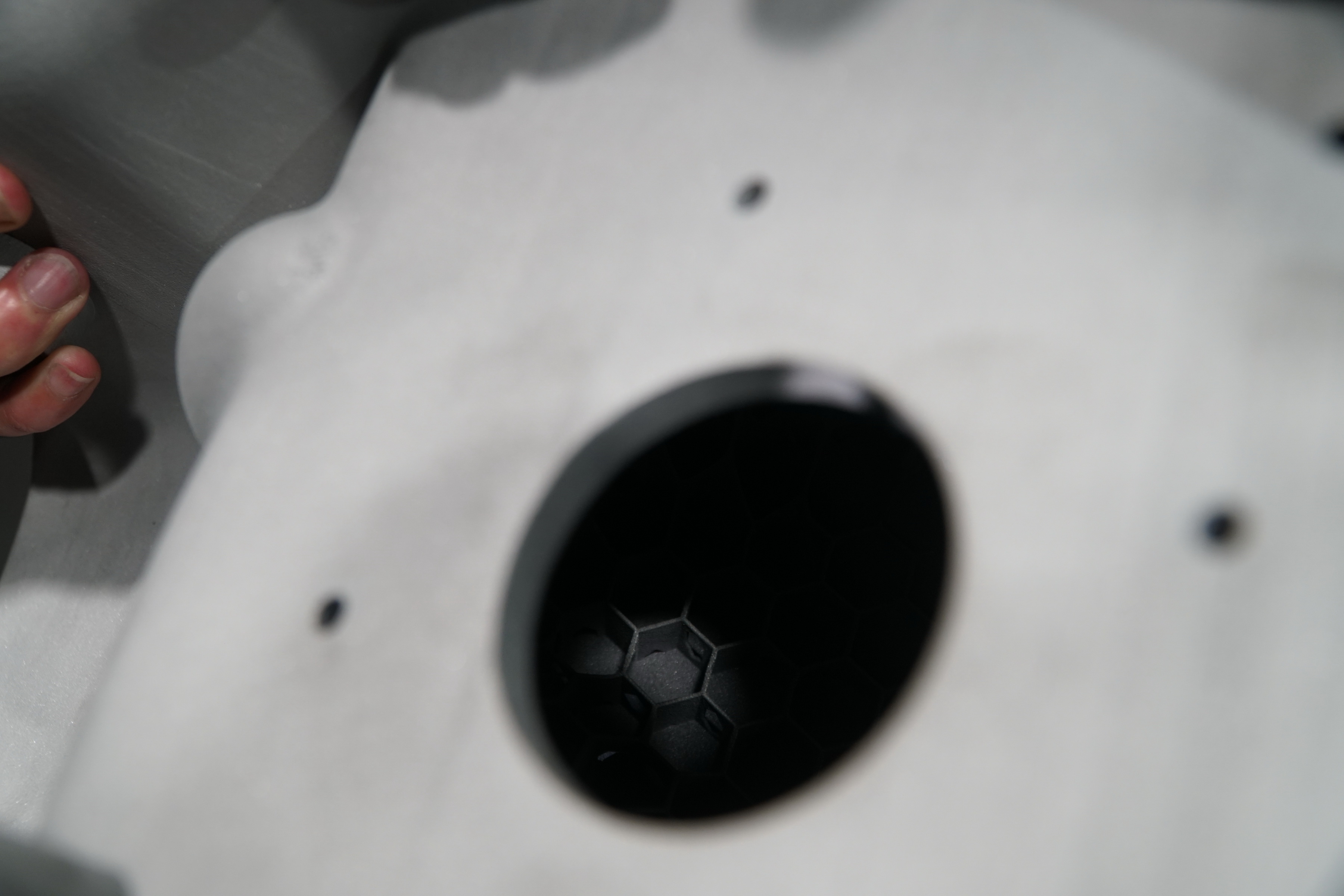